No cenário de manufatura em constante evolução, o conceito de fábrica inteligente emergiu como um elemento transformador para empresas que buscam otimizar suas operações e se manter à frente da concorrência. No centro dessa transformação está o sistema Smart Factory de Gestão das Operações de Manufatura (MOM), que oferece uma variedade de funcionalidades poderosas para executar os processos, aumentar a eficiência e impulsionar a inovação.
Neste post do nosso blog, vamos fazer uma análise aprofundada de um dos módulos críticos do sistema Smart Factory MOM, o módulo de Programação. Ao explorar suas aplicações práticas, nosso objetivo é mostrar como esse módulo pode revolucionar a programação e a execução da produção, permitindo que os fabricantes alcancem seus objetivos operacionais de forma adequada.
Mas antes de nos aprofundarmos nas complexidades do módulo de Programação, vamos entender a essência do Smart Factory MOM e como ele capacita os fabricantes a otimizar suas operações. Desenvolvida pela eWorkplace Manufacturing Inc., a solução Smart Factory MOM é uma plataforma configurável e de fácil integração que utiliza funcionalidades baseadas na nuvem para impulsionar a eficiência, sustentabilidade e inovação em toda a organização.
O Smart Factory MOM foi projetado para atuar nos desafios comuns enfrentados pelos fabricantes, como sistemas manuais de coleta de dados, dependência de planilhas, problemas de qualidade, questões de gestão de ativos e da força de trabalho, complexidades de regulamentações e muito mais. Com foco na solução de problemas e na melhoria contínua, essa solução permite que as empresas alcancem a produção inteligente, otimizando a eficiência, aumentando a produtividade, garantindo visibilidade e minimizando o desperdício.
Para alcançar esses objetivos, o Smart Factory MOM emprega quatro etapas chaves:
Visualizar, Simular, Executar e Adquirir.
- O componente Visualizar fornece aos tomadores de decisão e às equipes de produção insights em tempo real sobre os processos, oferecendo maior visibilidade e conhecimento.
- Através da etapa Simular, os fabricantes podem antecipar e responder rapidamente a mudança de variáveis, necessidades de mercado e demandas dos clientes, utilizando a capacidade de simulação.
- A etapa de Executar capacita os fabricantes a tomar decisões informadas, otimizar a utilização de ativos e colaboradores, reduzir os custos de produção, diminuir o tempo de entrega e minimizar o desperdício.
- Por fim, a funcionalidade Adquirir permite uma conectividade perfeita com máquinas e dispositivos de automação, facilitando a gestão centralizada de dados e aprimorando a produtividade e o desempenho no chão de fábrica.
Agora que definimos a importância do sistema Smart Factory MOM, vamos direcionar nossa atenção para o módulo de Programação. Essa etapa crítica desempenha papel fundamental na programação e na execução da produção de forma eficiente.
Módulo de Programação: Propósito e Importância
O módulo de Programação é uma parte integrante do Smart Factory MOM. O módulo de Programação utiliza um sofisticado sistema de programação avançado chamado Opcenter Scheduling (SC). Esse sistema avançado de programação opera por meio de uma abordagem baseada em restrições, permitindo a geração de programas de produção de forma integrada e computadorizada.
O objetivo do módulo de Programação é permitir que os fabricantes otimizem seu sequenciamento incorporando todos os requisitos e objetivos da programação em um mecanismo centralizado. Isso garante que as atividades de produção sejam planejadas e coordenadas estrategicamente para maximizar a eficiência e a utilização de recursos. Além disso, o módulo de Programação permite modificações na programação ao longo do dia, possibilitando ajustes em tempo real em resposta a mudanças nas condições fabris.
Pronto para adicionar o Smart Factory ao seu portfólio e se diferenciar dos concorrentes? Agende um horário conosco hoje para discutir como podemos fazer parceria!
Marque uma consulta
Como o módulo de Programação permita realizar uma programação de capacidade finita?
A programação da produção eficiente e o atendimento à demanda dos clientes são cruciais para às indústrias no atual mercado competitivo. No entanto, muitos fabricantes enfrentam dificuldades em avaliar com precisão sua capacidade produtiva e otimizar suas operações apropriadamente. Para enfrentar esse desafio, implementar a programação de capacidade finita é fundamental.
Vamos analisar um problema de manufatura, a solução para ele e como as indústrias podem aproveitar o módulo de Programação para alcançar uma programação eficiente e aprimorar seu desempenho operacional.
O Problema de Manufatura
As indústrias possuem um desafio crítico ao atender à demanda dos clientes e garantir processos de produção eficientes. Muitas vezes, elas têm dificuldade em avaliar com precisão sua capacidade produtiva e produzir de forma eficiente dentro das restrições de capacidade. Não conseguir atender os pedidos de venda em tempo hábil se torna um problema comum. As empresas precisam de uma solução que possa calcular sua capacidade produtiva e permitir que a demanda dos clientes seja atendida de adequadamente.
A Solução: Programação de Capacidade Finita em uma Fábrica Inteligente
Para superar esses desafios, os fabricantes podem implementar uma programação de capacidade finita como a solução definitiva. A programação de capacidade finita considera restrições de capacidade predefinidas, como horas de trabalho, turnos e horas de operação das máquinas. Ao utilizar o módulo de Programação, as indústrias podem otimizar sua programação da produção com base em informações de capacidade confiáveis e em tempo real.
Como as empresas podem utilizar a programação de capacidade finita através do módulo de Programação no Smart Factory MOM?
1. Definir com Precisão a Capacidade de Máquinas e Colaboradores
O módulo de Programação no Smart Factory MOM permite que as indústrias definam claramente a capacidade disponível de suas máquinas e funcionários. Essa definição exata da capacidade elimina o planejamento com base em suposições e garante um sequenciamento da produção factível.
2. Considerar Restrições de Recursos
O módulo de Programação incorpora restrições de recursos no processo de sequenciamento. Ele leva em consideração fatores como disponibilidade de máquinas, turnos dos funcionários, intervalos para refeição e tempo de parada permitido. Ao considerar essas restrições, os fabricantes conseguem programar as operações de acordo com a correta disponibilidade dos recursos, evitando sobrecarga e gargalos.
3. Otimizar Programação e Priorizar Clientes
Com a programação de capacidade finita, os fabricantes podem otimizar a programação de produção utilizando as horas produtivas de forma mais eficiente. O módulo de Programação ajuda a alocar os recursos de maneira eficaz, priorizando clientes com base na disponibilidade de recursos. Isso permite que os fabricantes otimizem os processos, aloquem os recursos adequadamente e melhorem a eficiência geral da produção.
4. Prevenir Problemas e Aprimorar o Controle de Custos
As indústrias podem prever e mitigar potenciais problemas que possam surgir devido a um planejamento de capacidade inadequado. Essa abordagem proativa garante que os prazos de entrega sejam cumpridos e minimiza o risco de ruptura de estoque. Além disso, os dados de produção coletados por meio do módulo ajudam as empresas a melhorar o controle de custos e otimizar a utilização dos recursos.
5. Aprimorar a Experiência do Cliente e Entregas
A programação de capacidade finita permite que os fabricantes ofereçam uma melhor experiência ao cliente, cumprindo prazos de entrega de forma consistente. O módulo de Programação ajuda a otimizar os processos, evitar atrasos e suportar entregas mais rápidas. O compartilhamento de dados precisos de produção com os clientes melhora a transparência e constrói confiança.
Gráfico de Gantt: Um caminho para a programação
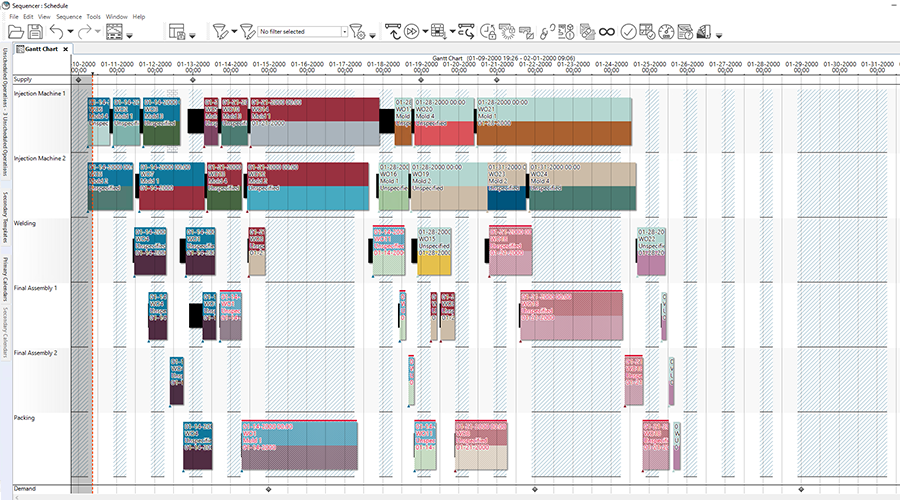
Na busca por uma programação da produção eficiente e uma utilização otimizada de recursos, o módulo de Programação oferece uma ferramenta valiosa, conhecida como gráfico de Gantt. O gráfico de Gantt representa visualmente a programação da produção, exibindo tarefas, recursos e suas respectivas linhas do tempo. Ele desempenha um papel crucial ao ajudar as indústrias a trabalharem com a programação de capacidade finita de maneira simples e eficaz. Alguns pontos-chave sobre o gráfico de Gantt incluem:
1. Visualização da Programação
O gráfico de Gantt fornece às indústrias uma visualização clara e intuitiva da programação da produção. Ele exibe as tarefas, seus horários de início e término, dependências e alocações de recursos. Com essa representação visual, os fabricantes podem facilmente compreender o carregamento dos recursos ao longo da linha do tempo, identificar caminhos críticos e reajustar o sequenciamento.
2. Utilização Eficiente de Recursos
A programação de capacidade finita considera os recursos disponíveis e suas capacidades ao criar uma programação. O gráfico de Gantt no módulo de Programação permite que os fabricantes aloquem recursos com precisão. O gráfico de Gantt ajuda a identificar sobrecargas, gargalos ou recursos subutilizados, representando visualmente a utilização de recursos ao longo do tempo e das tarefas. Os fabricantes podem tomar decisões informadas para equilibrar as cargas de trabalho, ajustar programas e otimizar a alocação dos recursos fabris, garantindo o uso eficiente da capacidade existente.
3. Ajustes Interativos na Programação
Uma das principais vantagens do gráfico de Gantt é sua natureza interativa. As empresas podem modificar o programa diretamente no gráfico, fazendo ajustes com base em dados em tempo real ou mudanças de prioridades. Ao arrastar e soltar tarefas ou ajustar suas durações, os fabricantes podem avaliar diferentes cenários, simular situações hipotéticas e realizar alterações dinâmicas na programação. Essa flexibilidade permite que as indústrias respondam a eventos inesperados, pedidos urgentes ou restrições de recursos, mantendo o balanceamento geral da programação.
4. Análise do Caminho Crítico
O gráfico de Gantt fornece uma análise do caminho crítico, destacando as tarefas ou sequências de tarefas que determinam o prazo final de produção de certas ordens de produção. Ao identificar o caminho crítico, as empresas podem concentrar seus esforços em garantir que essas tarefas sejam executadas de forma eficiente e sem atrasos.
5. Colaboração e Comunicação
O gráfico de Gantt é uma ferramenta de comunicação e colaboração dentro do sistema Smart Factory MOM. Ele permite que as partes interessadas, incluindo gerentes de produção, operadores e outros membros da equipe, visualizem e discutam a programação. Ao compartilhar o gráfico de Gantt, todos os envolvidos obtêm uma compreensão compartilhada da linha do tempo, alocação de recursos e dependências. Isso facilita uma melhor coordenação, tomada de decisões e colaboração interfuncional, promovendo um ambiente de produção mais ágil e responsivo.
Habilidades do APS: Exemplo do Mundo Real
A Siemens, líder global em tecnologia industrial, enfrentou desafios na otimização da produtividade de seu centro de tratamento de superfície de vagões ferroviários. A Siemens utilizou o Opcenter APS, solução avançada de planejamento e programação, para acelerar o tempo de produção, reduzir gargalos e evitar atrasos nas entregas. Ao integrar a programação avançada em seu processo de produção digital e aumentar o nível de detalhe no processo, a Siemens buscou coordenar o controle do fluxo de produção e melhorar a produtividade geral. Este estudo de caso destaca os desafios enfrentados, os principais fatores de sucesso na implementação do Opcenter APS e os resultados alcançados.
Desafios:
A Siemens identificou diversos desafios em seu centro de tratamento de superfície de vagões ferroviários. Eles precisavam acelerar o tempo de produção dos tratamentos de superfície dos vagões ferroviários, reduzir gargalos no processo de fabricação e garantir entregas no prazo. Esses desafios exigiam uma solução robusta para otimizar a programação e a coordenação em toda a linha de produção.
Fatores-chave para o sucesso:
Para superar os desafios, a Siemens implementou o Opcenter APS. Os seguintes pontos desempenharam papel fundamental no seu sucesso:
1. Integração da Programação
O Opcenter APS integrou suavemente a programação ao processo de produção digital da Siemens. Isso permitiu a coordenação em tempo real das atividades e a utilização eficiente dos recursos, otimizando o fluxo geral de fabricação.
2. Detalhamento do Processo
A Siemens aumentou o nível de detalhe do seu processo de programação. Ao incorporar dados mais detalhados, eles obtiveram melhor visibilidade das operações de fabricação e puderam tomar decisões de programação mais consistentes.
3. Controle e Coordenação do Fluxo de Produção
O Opcenter APS permitiu que a Siemens coordenasse os dados de fluxo de produção com os tempos de processamento e secagem. Essa sincronização garantiu um progresso suave nas várias etapas de trabalho envolvidas no tratamento de superfície de vagões ferroviários, minimizando o tempo ocioso e maximizando a produtividade.
Resultados:
A implementação do Opcenter APS proporcionou melhorias significativas no centro de tratamento de superfície de vagões ferroviários da Siemens. Os principais resultados conquistados incluem:
1. Redução de Atividades Sem Agregação de Valor
Com o Opcenter APS, a Siemens reduziu em 60% as atividades sem valor agregado e em 10% o tempo de preparação de máquina. Essa otimização tornou o processo de fabricação mais eficiente, economizando tempo e recursos.
2. Aumento da Produtividade e Eficiência
A implementação bem-sucedida do Opcenter APS permitiu que a Siemens obtivesse melhorias notáveis em produtividade e eficiência. Com a programação otimizada, eles puderam atingir as metas de produção de forma mais consistente e eficiente.
3. Redução de Custos
Por meio de uma programação e coordenação precisas, a Siemens experimentou uma redução nos custos de não conformidade. Os programas precisos permitiram uma melhor alocação de recursos, minimizando interrupções e retrabalho.
Considerações Finais
O módulo de Programação no Smart Factory MOM possui o sistema Opcenter APS sendo fundamental para ajudar as indústrias a obterem programas de produção otimizados de forma mais rápida e eficaz. Ao utilizar dados em tempo real, operações simplificadas e maior agilidade na geração do sequenciamento, os recursos do Opcenter APS atuam na superação dos desafios de produção das indústrias, aumentando a eficiência e oferecendo maior satisfação do cliente. Aproveitar os recursos do Opcenter APS dentro do Smart Factory MOM é uma decisão estratégica para as indústrias se manterem à frente da concorrência e prosperarem na era das fábricas inteligentes.
Pronto para adicionar o Smart Factory ao seu portfólio e se diferenciar dos concorrentes? Agende um horário conosco hoje para discutir como podemos fazer parceria!
Marque uma consulta