In today’s fast-paced and highly competitive manufacturing landscape, companies are under immense pressure to enhance production efficiency and meet ’consumers’ ever-growing demands. The changing market dynamics and consumer expectations have necessitated smaller production runs and a wider range of innovative products. Consequently, manufacturers are confronted with increasing production line changeovers, requiring seamless adaptation of processes, people, and equipment.
However, with the current economic climate discouraging capital investments in new equipment, manufacturers must seek improved changeover procedures to optimize their operations. Speed becomes a critical enabler as the number of changeovers a plant can perform is limited by the time allocated to each changeover. Many plants today devote significant time to changeovers, leading to non-production time and higher costs per unit. Manual processes further exacerbate the challenges, as they are time-consuming and prone to increased quality risks. Additionally, training operators to execute new changeovers consistently adds to the time required for transitions.
This blog explores how real companies have successfully addressed these challenges by leveraging electronic work instructions, electronic standard operating procedures (eSOPs), and Operating Method Sheet Sheets (OMS) to effectively guide operators through changeover processes. By utilizing electronic work instructions, manufacturers can achieve the agility and speed necessary to produce diverse products on the same production line without experiencing delays during changeovers. This, in turn, allows for the recovery of valuable manufacturing time, ensures consistent product quality, and reduces excess inventory—all of which are critical to improving the bottom line.
What is a Changeover Process?
In the manufacturing industry, a changeover process refers to the transition between producing one product or variant to another on a production line or machine. It involves reconfiguring the equipment, adjusting settings, and making necessary changes to accommodate the production of a different product.
Changeovers are necessary when manufacturers need to switch from producing one product or variant to another. This could be due to factors such as changes in customer demand, market trends, or the introduction of new product variations.
The changeover process typically begins with thoroughly analyzing the current production setup. This involves identifying the specific equipment, tools, and settings that need to be modified or reconfigured. Manufacturers may also need to consider factors such as material requirements, production capacity, and any potential impact on the overall production schedule.
Once the necessary changes have been identified, the actual changeover process begins. This typically involves stopping the production line or machine to allow for adjustments to be made. Equipment may need to be physically repositioned, parts to be replaced or modified, and settings to be recalibrated. Additionally, any necessary software or programming changes may need to be implemented to ensure smooth operation and compatibility with the new product or variant.
During the changeover process, manufacturers must also consider the potential impact on productivity and downtime. Minimizing the time required for changeovers is crucial to maintaining efficient production and meeting customer demands. Furthermore, effective changeovers require clear communication and coordination among various departments within the manufacturing facility. This includes production personnel, maintenance teams, engineers, and quality control staff. By collaborating and sharing information, manufacturers can ensure that all necessary changes are made accurately and efficiently.
Why Are Changeovers a Big Deal?
Changeovers have become a significant concern for companies due to their impact on costs, productivity, and overall operational efficiency. What was once considered a hidden cost in the base production, changeovers now act as a growing expense as their frequency increases and production runs are shortened to minimize inventory levels.
According to a survey conducted among Food Manufacturing readers, a majority of plants (57%) reported running two or three different products on a single production line per day. Furthermore, 30% of respondents indicated that changeovers involved transitioning to entirely different products, and 17% reported performing more than ten packaging changes daily.
Changeovers translate into non-production time, with labor hours dedicated to activities such as cleaning, adjusting, and verifying machine setups. They also pose greater risks, as inadequately-addressed issues during changeovers can lead to longer startup cycles, higher product rejection rates, and increased machine malfunctions. The more frequently changeovers occur, the higher the likelihood of experiencing these negative effects.
For instance, consider a manufacturer that adjusted its production run, halving the quantity of each product to create a more flexible inventory. While this change allowed for more diverse flavors and sizes on the line, it also led to a significant increase in changeovers—from one per week to six per week. As a result, the plant experienced a doubled equipment failure rate, which disrupted production, caused a surge in rejected products, and forced the company to rely heavily on operator overtime.
How Can You Enable Rapid Line Changeovers?
To enable rapid line changeovers and drive increased productivity, manufacturers must embrace the power of information and leverage eSOPs or OMS to systematize best practices. These digital solutions provide valuable insights and critical visibility into changeover processes, including accurate time measurements, identification of issues, and areas for improvement, thereby facilitating effective production planning.
For example, a food manufacturer implemented an eSOPs/OMS solution and empowered its process improvement team to analyze the data. Through this analysis, the team discovered that the same tasks took different amounts of time to complete, depending on the operator shift. This highlighted the need for better training to ensure consistency and efficiency. Additionally, the manufacturer found that transitioning through the production mix was smoother and quicker in one direction compared to others. For instance, reducing bottle size proved faster and easier than increasing bottle size.
Armed with valuable insights from electronic work instructions, the company made strategic changes. It provided additional training to operators and modified its production sequence to go from the largest bottle size to the smallest. This simple adjustment resulted in a remarkable 35% reduction in the overall time required for a line changeover. The significant improvement led to reduced operator overtime, fewer product rejects and minimized equipment failures, ultimately driving speed and production efficiency.
Ensuring high product quality is another vital aspect of rapid line changeovers. Many companies have recognized that operators play a critical role in maintaining quality standards and have shifted towards empowering operators to perform quality verification steps. Electronic work instructions, or OMS, prove invaluable in this regard.
For instance, one company experienced a negative impact on product quality due to changeovers. To mitigate this, the company implemented electronic work instructions to ensure that operators followed all necessary changeover steps meticulously. The digital workflows prevented operators from inadvertently skipping crucial steps, guaranteeing compliance with defined processes and minimizing setup errors that could result in rejected products.
Furthermore, the electronic work instructions enforced the collection of critical parameters throughout the changeover process, which could be automatically verified against quality standards. This proactive approach ensured that the production line was set up correctly and ready to run. With access to real-time information on product quality, operators could swiftly respond to any issues that arose, enabling tighter control without the need for additional manpower. As a result, the company experienced less rejection rates and maintained higher product quality standards.
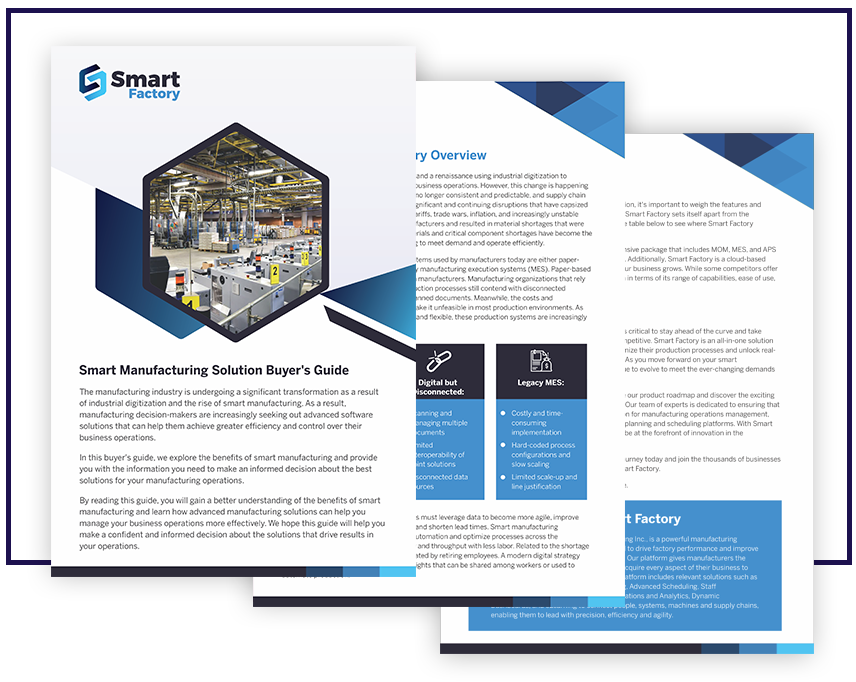
Why Are eSOPs Better Than Paper-Based SOPs?
The transition from paper to digital workflows brings numerous benefits that enhance operational efficiency, accuracy, and compliance. Here are some key advantages of utilizing eSOPs:
1. Strong Adherence to Standard Operating Procedures
eSOPs ensure that lessons learned and best practices are effectively implemented and followed. By digitizing SOPs, companies can establish clear guidelines and standardized processes that are easily accessible to operators.
2. Improved Accuracy and Repeatability
Compared to paper-based SOPs, eSOPs offer a higher level of accuracy and repeatability. Digital workflows leave less room for interpretation or abuse, whether intentional or unintentional. With eSOPs, operators can access precise instructions, eliminating potential errors caused by misinterpretation or inconsistent execution.
3. Direct Link to Plant Operations
eSOPs can be integrated with the plant’s equipment and control systems, ensuring a direct link between instructions and operations. This integration helps maintain safety interlocks and enforces changeovers to be executed in the specified sequence. By connecting eSOPs to the plant environment, companies can minimize the risk of compromising safety measures and achieve seamless coordination between digital instructions and production processes.
4. Efficient Data Collection and Collation
One of the challenges of paper-based SOPs is the cumbersome task of manually collecting and collating large volumes of data. eSOPs streamline this process by automating data collection, making it easier to capture relevant information during changeovers. The digital format enables real-time data capture, reducing the likelihood of errors and facilitating efficient data analysis for continuous improvement initiatives.
5. Powerful Reporting and Decision-Making Tools
eSOPs provide powerful reporting tools that transform raw data into meaningful information. This information can be consumed by organizational stakeholders, facilitating better decision-making. By leveraging analytics and visualization capabilities, eSOPs enable companies to identify trends, analyze performance metrics, and make data-driven decisions to optimize changeover processes and overall operations.
How Do eSOPs/OMS in Smart Factory MOM Help Improve Changeover Processes?
The implementation of eSOPs or OMS within the Smart Factory MOM system offers significant improvements to changeover processes. Manufacturers can streamline changeovers and achieve operational excellence by leveraging digital tools and workflows. Here’s how eSOPs or OMS in the Smart Factory MOM solution contribute to enhancing changeover processes:
- Standardization: eSOPs or OMS enable the establishment of standardized procedures for changeovers. Manufacturers ensure consistency and eliminate variability in changeover processes by documenting and digitizing step-by-step instructions. Standardization reduces errors, minimizes rework, and optimizes setup time, improving efficiency.
- Training and Knowledge Transfer: Operating Method Sheets or eSOPs within a Smart Factory MOM system serve as valuable training materials. New operators can quickly learn the changeover process by following detailed instructions. Moreover, these digital workflows facilitate knowledge transfer among team members, ensuring that best practices are consistently followed across shifts and personnel changes.
- Visual Aids and Digital Assistance: Smart Factory MOM system leverages visual aids, such as images, videos, or 3D models, to enhance understanding and clarity during changeovers. Operators can visualize the required step that minimizes confusion and errors. Additionally, digital assistance features embedded within the system provide real-time prompts, alerts, and guided workflows, ensuring operators perform each step accurately and efficiently.
- Real-time Data Capture and Analysis: ESOPs in the Smart Factory MOM system enable real-time data capture during changeovers. This data encompasses setup times, efficiency metrics, and potential bottlenecks. By collecting and analyzing this information, manufacturers gain valuable insights into the performance of changeover processes. They can identify areas for improvement, optimizing setup times, and promptly address any inefficiencies or delays.
- Continuous Improvement: Smart Factory MOM system facilitates continuous improvement efforts in changeover processes. Operators can provide feedback, suggestions, and observations directly within the system, allowing for ongoing refinement of SOPs. This iterative approach ensures that changeover processes are continuously optimized, resulting in streamlined operations and increased productivity over time.
Wrapping Up
In today’s dynamic manufacturing landscape, keeping up with consumer demands for diverse products challenges manufacturers. Smaller production runs and multiple products per line daily have led to an increased frequency of line changeovers, resulting in non-production time, quality issues, and rising costs.
Fortunately, leading companies have found a solution with eSOPs or OMS, to expedite line changeovers while maintaining quality. By guiding operators through changeover processes with clear instructions, manufacturers can enhance machine and recipe setup speed and accuracy. This, in turn, enables efficient production of diverse products on the same line, eliminating delays and errors during changeovers. As a result, valuable production time is reclaimed, and consistent product quality is ensured.
Moreover, adopting electronic work instructions facilitates rapid and reliable changeovers, providing manufacturers with improved predictability. This, in turn, drives proactive resource planning, including reducing excess inventory. Manufacturers can enhance agility across the plant by gaining critical insights into real-time production data, resulting in accelerated profit margins and a stronger bottom line.
As the manufacturing industry evolves, electronic work instructions will play a vital role in driving efficiency, enhancing quality, and ensuring profitability. By leveraging the power of eSOPs, manufacturers can navigate the complexities of changeovers, unlock the potential of their smart factory, and drive success in the increasingly demanding and competitive marketplace.
Ready to add Smart Factory to your portfolio and differentiate yourself from competitors? Schedule an appointment with us today to discuss how we can partner up!