Key Components of Manufacturing Operations Management
Manufacturing Operations Management (MOM) is the revolutionary solution that every manufacturing company must have. It is the backbone of an enterprise and comes with a series of operative programs that make production efficient and effective. It may include crucial components such as production planning, scheduling, inventory management, quality control, maintenance, and resource allocation. Utilizing these key components can help you stay ahead of the competition. Explore what makes MOM have significant impact on the modern manufacturing world.
Production Planning

Objective Handling
A MOM solution allows the manufacturer to efficiently handle day-to-day production to ensure the high-level production objectives are met over time. It ensures asset utilization, increases production output and reduces cycle time. It collaborates resources, deadlines, and various production processes for efficiency, cost-effectiveness, and customer satisfaction.

Capacity Planning
As vital as it is to understand customer demand, knowing the amount to produce is also critically important. Manufacturing scheduling software builds on the power of the facility. Smart Factory helps to evaluate the capacity of the production unit. It assesses available resources including labor, machines, and productivity for better resource allocation and production planning.

Demand Forecasting
One aspect of production planning and scheduling software is to decipher demand. Demand forecasting involves analyzing data, market trends, and client insights to produce the markets' future outlines. A MOM solution with advanced scheduling capabilities creates production schedules that accurately match client orders. It helps to reduce order wastage and ensure sufficient inventory is on hand. The spike in real-time connectivity boosts the production process and leads to better decisions and valid responses to production crises.
Production Scheduling
- It helps use resources efficiently and carry out the production plan meticulously by maximizing utilization and reducing costs.
- With real-time demand analysis and predictions, it aids in informed and data-driven decision-making and boosts efficiency.
- It reduces lead times, delights and satisfies the customer by ensuring the best schedule for the production plan.
- It plans the capacity and boosts productivity. It takes an active role in inventory management, lowers waste, and minimizes deadlines.
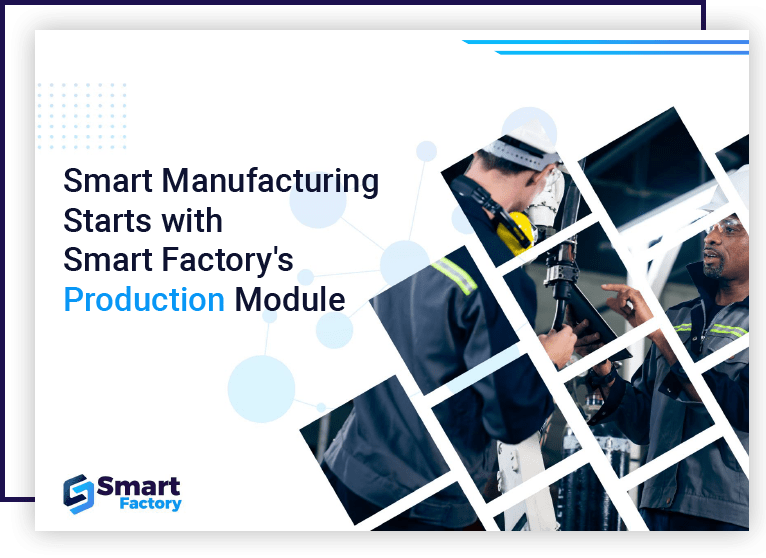
Ready to optimize your production scheduling?
Inventory Management
- Demand and Supply
- Cost Control
- Customer Satisfaction
Quality Control in MOM
- Visual checks to review and guarantee that no visual defects or irregularities are in the product.
- Dimensional checks to see if every product is of the same size and has the same structural geometry.
- Functional checking to assess the product functionality against the predefined production criteria.
- Non-destructive testing is usually done via X-rays or ultrasounds to scan for defects without damaging the products.
- Destructive testing by intentionally damaging one sample product to ensure the materials and design meet the necessary standards.
Maintenance in Manufacturing
Resource Allocation
Inventory Allocation
- It includes inventory management that ensures the right inventory is on hand to meet the needs of changing market demand.
- It guarantees efficient use of raw and in-progress materials to ensure no waste or underproduction.
- A MOM solution tracks the fluctuating market conditions to derive data and then allocates the resources.
Labor Allocation
- It ensures matching the right personnel to the right task in the manufacturing unit.
- It considers skill sets, experience, and workload balancing before allocating work to an individual.
- It matches production workers with the most suitable tasks, to reduce errors and enhance productivity.
Equipment Allocation
- An effective MOM solution uses every machine to achieve the greatest benefit for the business.
- It optimizes equipment by considering availability, inspection and maintenance cycles, production needs, and more.
- Proper allocation ensures the machine is used to its maximum potential.