Are you finding it challenging to maintain a sufficient quantity of stocked goods? It’s possible that the growing demand has put you behind schedule, and your lead time is gradually getting longer with every fulfillment. Alternatively, you may have finished goods that are taking up space and aren’t selling as well. It’s time to assess your inventory management procedures if any of these problems seem familiar to you.
What is Inventory?
Inventory refers to the items and supplies that a business uses in manufacturing or sales. Accurate inventory management is crucial for businesses to effectively and efficiently manage their resources. Quantity, value, and stock location are just a few of the data points that inventory accounting covers and records. This information enables businesses to make more informed decisions regarding sales, purchasing, and production.
The process of keeping an eye on and managing inventory levels is known as inventory techniques. Examples of such tasks include order planning, warehousing, and transportation. Businesses that practice effective stock management ensure they have the appropriate amount of product to satisfy consumer demand. Optimizing production processes and reducing waste are other benefits.
Depending on the type of inventory and the company’s accounting requirements, a specific approach may be more suitable. Manual inventory management systems, periodic inventory management systems, and perpetual inventory management systems are types of inventory management systems.
For organizations, inventory is a vital resource that significantly impacts financial reports. Having precise and current records of inventory levels is crucial for this reason. Maintaining accurate inventory levels in accounting records can be achieved through routine stocktaking.
What Makes Inventory Management Crucial?
The health of a business depends on effective inventory management, as it reduces the possibility of stockouts and erroneous records by ensuring that there is rarely too much or too little stock on hand.
The Sarbanes-Oxley (SOX) Act and Securities and Exchange Commission (SEC) regulations require public corporations to maintain inventory records. Businesses need to record their management practices to demonstrate compliance.
Inventory Management’s Benefits
Inventory control ensures you can fulfill open or incoming orders and increases revenue, its two primary advantages. Additionally, inventory control:
Conserves Money:
Understanding stock trends helps you better utilize the stock you already have by enabling you to identify where and how much of each item you have on hand. Because you can pull inventory from anywhere to meet orders, you can also maintain less stock at each location (warehouse or shop). All of these factors reduce the expenses associated with inventory and the quantity of unsold stock before it becomes obsolete.
Boosts Cash Flow:
Cash flows through the business continuously when inventory is managed correctly, as you only spend money on products that sell.
Keeps Customers Happy:
Ensuring that customers promptly receive what they desire is one way to cultivate a devoted customer base.
Obstacles in Inventory Management
Having too much inventory and not being able to sell it, not having enough inventory to meet orders, and not knowing what you have in inventory and where it is situated are the main obstacles to inventory management. Additional challenges include:
Obtaining Precise Stock Information:
Determining which merchandise sells well or when to replenish stock is impossible without accurate stock details.
Subpar Procedures:
Manual or antiquated procedures can slow down operations and increase the risk of errors.
Shifting Needs of the Customer:
Consumer demands and preferences are ever-changing. How can you determine when and why their preferences change if your system cannot observe trends?
Making Good Use of Warehouse Space:
Employees spend time searching if similar products are challenging to find. Gaining expertise in inventory management can assist in removing this obstacle
Keeping Inventory Accounts
As a business typically intends to sell its finished goods within a year or less, inventory is considered a current asset. Before inventory can be included on a balance sheet, it must be physically counted or measured. Organizations generally employ advanced inventory management systems that track stock levels in real-time
One of three approaches accounts for inventory: weighted-average costing, last-in-first-out (LIFO), or first-in-first-out (FIFO) costing. An inventory account typically consists of four distinct categories:

Ingredients in raw form
Symbolizing the different kinds of materials that a business purchases for use in its production. These ingredients must undergo various processes before a business can transform them into a finished product ready for sale.

Work-in-process (or goods-in-process)
This approach is for components being processed into a final product.

Finalized products
These are finished goods that clients of a business may purchase.

Products
Symbolize completed products that a business purchases from a source to resell later.
Take a step towards smarter manufacturing today. Book a demo of Smart Factory MOM and discover how our solution can improve your factory’s efficiency, reduce downtime, and increase profitability.
What are the Inventory Management Techniques?
Tracking and controlling stock levels are critical components of contemporary inventory management strategies, which help companies fulfill consumer demands. To manage their inventory, businesses can employ a variety of strategies, including:
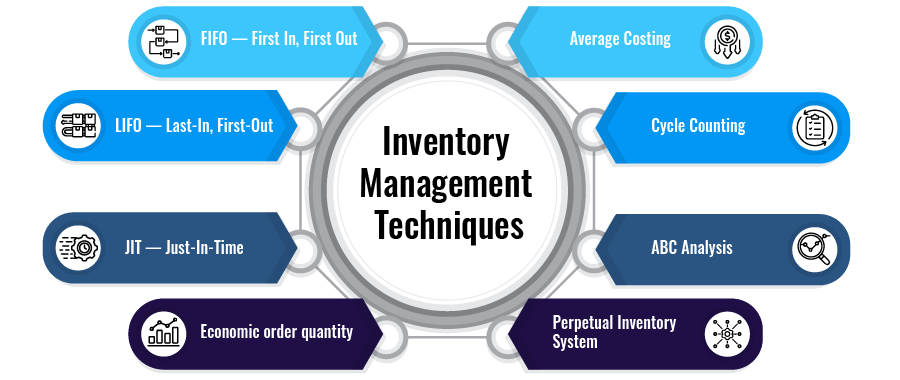
Depending on your unique requirements, selecting the most appropriate approach for your organization is crucial, as each strategy has pros and cons.
Several variables, such as the type of products you sell, client demand, and financial constraints, will determine the best approach for your company.
The successful operation of a business depends heavily on inventory management systems. Utilizing effective inventory management procedures can save carrying costs, cut waste, and boost productivity.
Manufacturing Approaches for Inventory Management
FIFO – First In, First Out
One of the most frequently utilized inventory management strategies in the manufacturing industry is FIFO.
This method reduces the risk of spoilage or obsolescence and ensures that the oldest products are used first. Assets are sold, utilized, or disposed of according to the order in which they are generated or acquired under the FIFO inventory valuation method. With this approach, an organization’s inventory costs and levels can be seen more clearly, which is why accounting often employs it.
LIFO – Last-In, First-Out
One way to determine the inventory cost for the cost of goods sold is to utilize the LIFO (Last-In, First-Out) technique.
The LIFO inventory valuation system ensures that the last items added to the inventory are sold first, as the name implies. Since the most recent purchases were made at the highest prices, higher expenses were allocated to commodities sold during periods of inflation. LIFO can result in lower taxes for firms due to the IRS’s ability to subtract the higher inventory expenses from taxable income.
JIT – Just in Time
Businesses using just-in-time (JIT) inventory only place orders for as much stock as is necessary to satisfy client demand at that moment.
Thanks to this approach, businesses will always have the products they need on hand, reducing holding expenses.
Under the Just-In-Time (JIT) system, companies place orders for raw materials from suppliers based on their production schedules. Ordering materials and components as needed helps businesses avoid the high expenses associated with maintaining an extensive inventory. Implementing JIT can increase overall profitability and efficiency for businesses.
Economic Order Quantity (EOQ)
Economic Order Quantity (EOQ) helps companies determine the optimal order quantity for their goods.
By considering various expense considerations, including holding and ordering costs, businesses can determine the most cost-effective approach to managing their stock levels. The order quantity that allows a business to order, receive, and maintain inventory at the lowest possible cost is known as the Economic Order Quantity (EOQ). The EOQ model takes into account the trade-off between the cost of carrying inventory and the cost of ordering inventory.
Standard Pricing
When utilizing the average cost, also known as the weighted-average approach, a manufacturer determines the cost of each item in inventory by dividing the overall cost of goods created or acquired during a specific time by the total number of items:
The formula for calculating the average cost of production: Total cost of production divided by the number of units produced.
Using this approach, the cost of each unit in stock is determined by averaging the expenses incurred in the production or acquisition of the units on sale.
Every inventory unit is then valued at the average cost per unit, calculated regularly, and typically done after each accounting period.
Counting Cycles
Physical inventory counts are employed in cycle counting to verify inventory checks and balances against records.
To accomplish this, producers must conduct routine inventory counts and document modifications for individual products. Cycle counting offers numerous advantages, including lowering the requirement for quarterly or annual inventory counts, identifying mistakes and inconsistencies early on, and providing precise information for decision-making. Furthermore, to avoid mistakes in the future, cycle counting can be used to pinpoint areas where procedures need improvement. When done correctly, cycle counting can be a beneficial method for inventory management.
ABC Analysis
Based on the importance of each item, ABC analysis, also known as ABC inventory management, establishes the value of your inventory.
ABC classifies products and rates them according to risk, cost, and demand. This analysis can be employed when deciding which inventory goods to stock, how much to stock, and when to place additional orders.
Perpetual System of Inventories
Utilizing computerized Point of Sale (POS) systems or Enterprise Resource Planning (ERP) manufacturing software, perpetual inventory systems, also known as live inventory management software, automatically record sales, purchases, and inventory utilization.
Businesses can make better judgments about ordering and selling products using this technology, which provides them with up-to-date information on inventory levels. Various approaches exist to install perpetual inventory systems depending on the company’s demands. For example, while some companies may choose to deploy point-of-sale systems in every retail store, others may opt to use them exclusively in specific areas or for particular product categories. Enterprise asset management software enables the monitoring and management of inventory levels across multiple sites.
Perpetual inventory systems offer numerous advantages over conventional inventory management tools and procedures. Their ability to provide organizations with real-time inventory level information helps avoid stockouts and lost sales, which may be the main advantage. Additionally, perpetual inventory systems offer better visibility into stock levels and turnover rates, assisting companies in lowering their overall inventory expenses.
What Distinguishes Inventory Management From Other Procedures?
Inventory management and related practices are occasionally confused by people. Inventory management encompasses all of a corporation’s stock. On the other hand, supply chain management oversees the entire process from the supplier to the point of product delivery to the customer, encompassing various components such as inventory control, warehouse management, and concerns stock in a particular area.
How Do I Select a System for Inventory Management?
Deciding on the features your company requires in an inventory management system is essential. Consider which tasks are more critical: planning inventory, keeping an eye on trends, or tracking stock movements and whereabouts within a warehouse?
The Bottom Line
Inventory management is an essential component of company operations, and its proper implementation is necessary depending on the type of business and the products it offers. Since each form of inventory management has advantages and disadvantages, there might not be a single ideal kind. However, employing the most appropriate inventory management strategy can be beneficial.
Utilize the Smart Factory MOM Solution to Implement Inventory Management and Gain Business Benefits
Decision-makers understand the need for an inventory management system that can expand with their business. The Smart Factory MOM Solution offers cloud-based inventory management solutions suitable for organizations of all sizes, incorporating features such as automated replenishment, lot tracing, and tracking in various locations.
Smart Factory’s feature set includes site planning, automated stock replenishment, lot and serial tracking, cycle counting, warehouse and fulfillment management, along with other native inventory management and control tools. Discover how Smart Factory can enhance cash flow, reduce handling costs, and automate the management of inventory.
Contact us today to learn more about how we can help you implement, train, and maintain the Smart Factory MOM solution and count on us to help you overcome any hurdles along the way.