What is a Quality Management System (QMS)?
Principles of Quality Management
- Planning with Quality: Quality management begins with setting clear objectives and a well-defined roadmap for achieving them. This includes identifying customer expectations and the standards that must be met.
- Quality Assurance: Ensuring that the processes, procedures, and resources are in place to consistently produce products or services that meet the established quality standards.
- Quality Control: It refers to the systematic examination and monitoring of processes and outputs to detect and correct any deviations from the defined quality standards. This includes methods such as inspections, testing, and data analysis.
- Enhancement of Quality: It refers to a commitment to continual improvement. This involves learning from past experiences, customer feedback, and the latest best practices to evolve and refine processes over time.
- Customer-Oriented: Meeting or exceeding customer expectations is paramount. Quality management focuses on understanding and fulfilling the needs of clients.
- Leadership: Effective leadership is crucial for creating a quality-driven culture within the organization. Leaders set the tone and direction for quality initiatives.
- Engaging People: Involving employees at all levels is essential. Engaged and motivated employees are more likely to contribute to quality improvement.
- Process Approach: Quality management emphasizes a process-oriented approach, where understanding, managing, and optimizing processes are vital for consistent quality.
- Continuous Improvement: The pursuit of ongoing improvement is a core principle. Identifying areas for enhancement and actively making changes lead to higher-quality outcomes.
- Evidence-Based Decision Making: Decisions should be driven by data and factual information. This ensures that choices are well-informed and based on evidence.
- Managing Relationships: Collaborating effectively with suppliers and stakeholders is essential. Strong relationships support the flow of resources and information, contributing to overall quality.
Advantages of Implementing a Quality Management System
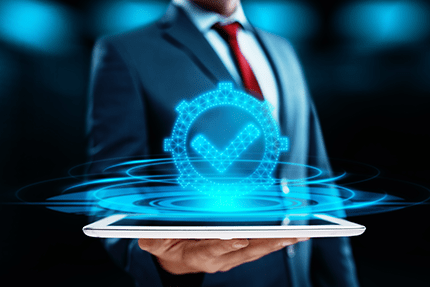
Enhanced Customer Satisfaction

Improved Productivity

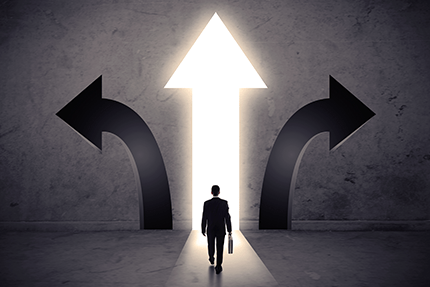
Enhanced Decision-Making
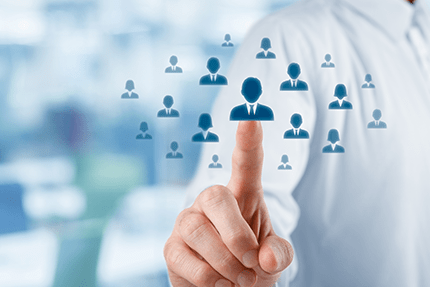
Increased Employee Engagement
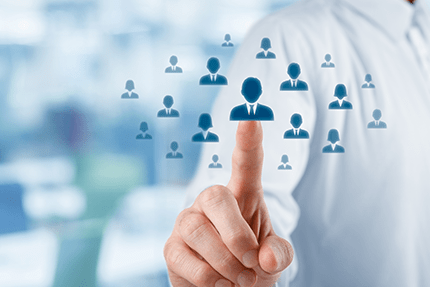
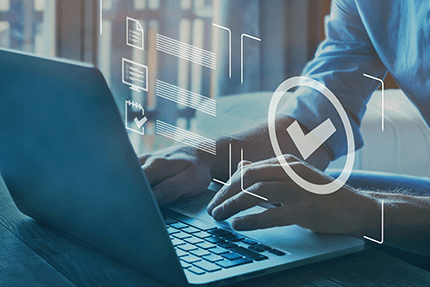
Regulatory Compliance
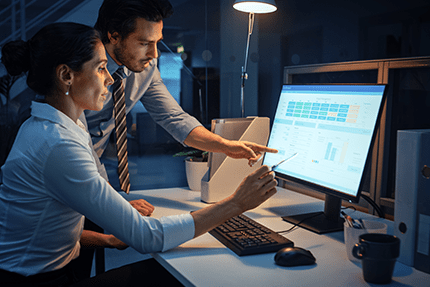
Effective Risk Management
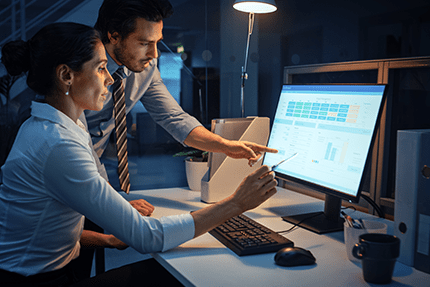
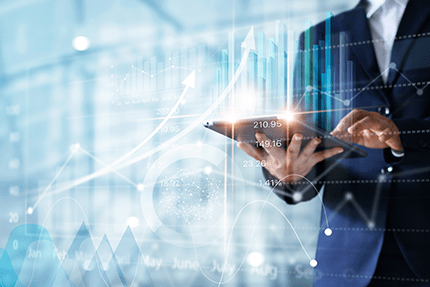
Continuous Improvement
Quality Management Methods
Standardized Methods: Any QMS that complies with a set of federal codes and regulations is considered standardized. Notable examples are the various ISO certifications:
- ISO 9000 Series
- ISO 14000 Series: Environmental Management
- ISO 13485: Medical Devices
- ISO 19011: Auditing Management Systems
- ISO/TS 16949: Automotive Management
Establishing and Implementing QMS
Design and Build: The design and build phases establish the framework, processes, and implementation strategies of a QMS. Senior management should oversee this phase to ensure that the systems align with the company’s and clients’ needs.
Deployment: Breaking down each process into smaller steps and providing personnel with training, documentation, education, and key performance indicators (KPIs) ensures that deployment is executed in a granular manner. Company intranets are increasingly facilitating the implementation of quality management systems.
Control and Measure: Measurement and control are integral to creating a QMS, achieved primarily through regular, systematic audits of the system. The specifics of measurement and control differ significantly between organizations, depending on factors such as size, potential risk, and environmental impact.
The Innovative OMS Feature in Smart Factory MOM
What is OMS?
Flexibility and Adaptation to Varied Scenarios
Key Features of OMS in Smart Factory MOM

Unlimited Process Customization
Manufacturers can define and execute unlimited processes, sections, and instructions, tailoring the system to their unique needs.

Time Management
OMS includes electronic chronometers and timers to record time and planned wait times within processes, enabling precise control over time-related factors.

Interactive Questions
OMS allows for the inclusion of open-ended and directed questions, with actions triggered by responses. This interactive element enhances the guidance provided to operators.

Transaction Recording
Transaction instructions are supported, enabling the recording of consumption and other critical transactional data.

Adaptive Actions
OMS enables the definition of mandatory and optional steps, as well as action restrictions based on responses, ensuring a flexible and adaptive process flow.

User-Friendly Interface
The system features a user-friendly interface for easy process assignment and utilization, reducing the learning curve for operators.

Version Control
Versioning and Engineering Change Notice (ECN) control for processes in electronic formats ensures that manufacturers can seamlessly manage process revisions.

Paperless Documentation
Electronic distribution of processes eliminates the need for paper-based documentation, contributing to a more sustainable and efficient manufacturing environment.

Conditional Branching
OMS supports processes with conditional branching and multiple execution paths, enabling manufacturers to address complex production scenarios.

Multimedia Integration
To enhance instructions, OMS offers multimedia support, including images, videos, text files, data tables, and more. This multimedia integration provides visual clarity and aids in comprehension.

Compliance and Traceability
OMS ensures compliance with process sections and enables dynamic traceability of processes. This is crucial for quality assurance and regulatory adherence.