Imagine navigating through a complex maze, encountering countless twists and turns, dead ends, and unexpected obstacles at every corner. This is not too dissimilar from the journey of a manufacturing organization facing the challenges inherent in its operations. The manufacturing maze can be daunting, from supply chain complexities to operational inefficiencies, quality control issues, and workforce management hurdles. However, in the face of these challenges lies the immense opportunity for growth and success. The key lies in finding effective solutions to overcome these obstacles, whether through corrective measures or harnessing the power of technology.
In this blog post, we will explore some of the most common challenges manufacturing factories and organizations face and unveil practical solutions that can lead to triumph in the manufacturing maze.
Challenge 1: The Risks of Over-Reliance
In the intricate world of manufacturing, a hidden challenge lurks within production planning, posing significant risks to the smooth functioning of operations. Imagine a manufacturing company that relies solely on the tacit knowledge of one individual, the Production Planner, to configure their production processes. This individual holds the key to the intricate planning process, possesses vital knowledge of the machines, and understands the intricate details of customer orders. Without them, the entire manufacturing process hangs in the balance, teetering on the edge of potential disaster.
Most manufacturing companies, unfortunately, lack documented procedures or backups for their production planning know-how. Instead, they heavily rely on the expertise and experience of the Production Planner. While this may seem like a convenient arrangement, it brings about a host of risks and vulnerabilities. In the event that the Production Planner is absent or leaves the company, the manufacturing process could grind to a sudden halt. The absence of their invaluable knowledge poses a substantial risk, leading to potential errors, increased downtime, and, ultimately, unhappy customers.
According to a study by the Manufacturing Advisory Service, over-reliance on individual knowledge in production planning is a challenge faced by many manufacturers. The study warns, “Relying on the knowledge of one person poses a significant risk to business continuity and competitiveness. If that person were to leave or be unable to perform their role, the entire manufacturing process could come to a standstill, resulting in delayed orders, increased errors, and dissatisfied customers.”
Compounding the challenge is the fact that the Production Planner is likely employing unreliable planning methods, such as spreadsheets and whiteboards, coupled with the tacit knowledge stored solely in their own mind. This reliance on manual, opaque methods creates a lack of visibility, making it difficult to analyze the effectiveness of the planning process. Without a reliable means of assessing how well the plan performed against actual output, the company finds itself unable to identify areas for improvement or optimize manufacturing operations.
Building schedules manually is not only time-consuming but also highly cumbersome when it comes to evaluating the efficiency of manufacturing operations. The absence of a structured and automated planning system leaves the company vulnerable to firefighting scenarios, leading to unnecessary delays. The lack of a reliable definition and backup plan increases the risk of blunders that can ultimately make the business less competitive in the market.
The Production Planner shoulders the responsibility of effectively scheduling the usage of production materials to ensure maximum output. They face the intricate task of assessing the timeliness of material supply and aligning it with production goals. However, due to the reliance on their unique process and knowledge, implementing the plan without their assistance becomes a challenge for others within the company.
This over-reliance on the detailed knowledge of one or a few individuals is a challenge still faced by many manufacturers today. It poses significant risks to their businesses’ stability, efficiency, and competitiveness.
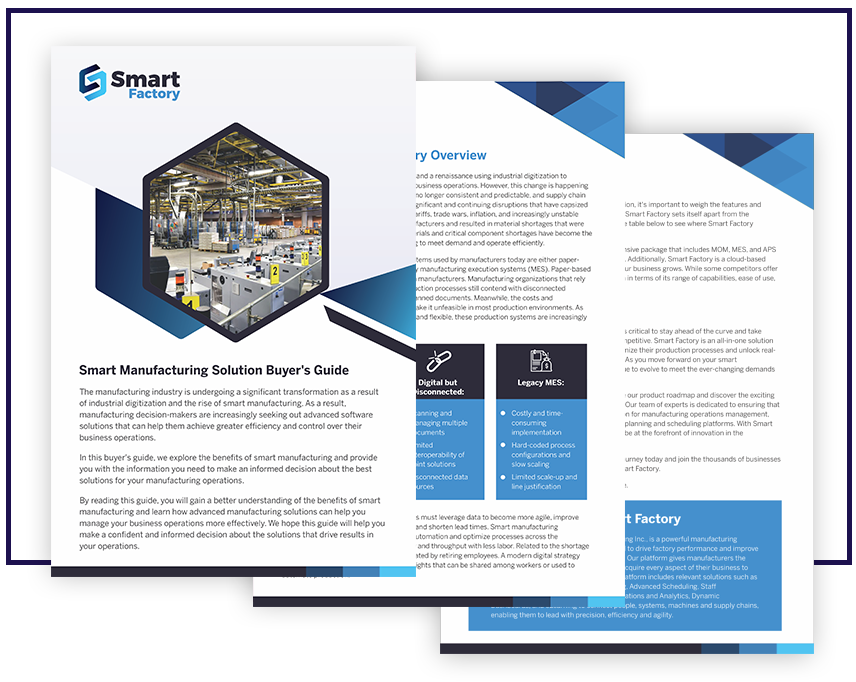
Optimize Your Production Process With Our Production Module
Solution: Embracing the Power of MES for Optimal Production Planning
To overcome the risks of over-reliance on individual knowledge in production planning, manufacturers can turn to a powerful solution: Manufacturing Execution Systems (MES). Smart Factory is a Manufacturing Operations Management (MOM) solution with MES and Advanced Planning and Scheduling capabilities. By leveraging the APS capabilities of the Smart Factory MOM, manufacturers can document and access critical knowledge, enabling the entire team to contribute and collaborate effectively. This mitigates the risk of relying solely on an individual’s tacit knowledge and paves the way for optimized scheduling and enhanced operational efficiency.
Translating the production planning knowledge into an APS solution within the MES ecosystem empowers manufacturers to create an optimized schedule seamlessly. Machine times, customer preferences, and process details can be configured into the APS tool, which then generates schedules based on pre-built constraints and priorities. This technology-driven approach alleviates the burden of manually assembling schedules, freeing up the Production Planner to focus on process optimization and strategic decision-making.
According to a study conducted by the Manufacturing Technology Centre, “Companies that adopt an MES solution witness a significant reduction in human errors and firefighting time, resulting in improved productivity and enhanced competitiveness. The accessibility of knowledge, data, and processes to the entire team facilitates smooth operations and enables quicker decision-making, leading to more streamlined production plans.”
The production plan housed within the MES solution provides an online visual representation of scheduled orders. It can be viewed in a Gantt chart format, showcasing activities and tasks against time, or in a user-friendly list format. This comprehensive view of the production plan ensures that the entire team, including shop floor workers, has access to real-time information and a clear understanding of their tasks and priorities. With the plan built on approved processes and data stored within the MES, everyone works together towards a common goal.
Challenge 2: Overcoming Inefficiencies in Manufacturing Reporting
In the dynamic manufacturing world, data is the key to unlocking valuable insights and driving informed decision-making. However, gaining meaningful insights from their operations can be daunting and time-consuming for many manufacturers. Most manufacturers struggle to extract and analyze the necessary data for their quarterly business reports.
They usually grapple with manual, paper-based processes that hinder their ability to efficiently track down the needed data. Hours are wasted scouring disparate sources of information, and even then, the presentation of the data becomes an arduous endeavor. As a result, manufacturers find it challenging to showcase operational improvements, demonstrate order fulfillment to customers, and identify areas of losses that require rectification.
Solution: Data-Driven Manufacturing Excellence With Smart Factory MOM
To address the inefficiencies in manufacturing reporting, the manufacturers must transition from manual, paper-based processes to a unified software solution that can effectively manage their operations and provide comprehensive data insights. One such solution is Smart Factory MOM, a powerful manufacturing system that offers a range of tools to simulate, execute, visualize, and acquire manufacturing operations.
By implementing Smart Factory MOM, manufacturers can consolidate their data into a single source of truth, ensuring that everyone in the organization stores production information in one centralized platform. This streamlines data management and eliminates the challenges associated with disparate sources of information.
Smart Factory MOM enables manufacturers to intelligently plan their output based on factors such as machine capabilities, customer preferences, and process details. Additionally, the solution facilitates real-time data collection from the shop floor, capturing crucial information on the performance of planned orders and any disparities between planned and actual output.
With Smart Factory MOM, manufacturers access a wealth of data-driven insights. The solution automatically calculates key performance metrics such as Overall Equipment Effectiveness (OEE) and Overall Labor Effectiveness (OLE), clearly understanding production efficiency. Real-time visibility into shop floor activities allows the manufacturer to monitor performance, identify issues, and take immediate corrective actions.
Furthermore, Smart Factory MOM empowers manufacturers to analyze manufacturing data through intuitive graphs and charts. These visual representations make it easy to identify loss areas, whether related to quality issues, specific machines, or significant time losses due to changeovers or maintenance. Armed with this information, manufacturers can make informed decisions to optimize production schedules and enhance overall factory efficiency.
As renowned manufacturing expert W. Edwards Deming once said, “In God we trust, all others bring data.” The adoption of Smart Factory MOM equips manufacturers with the data-driven insights necessary to drive operational excellence, reduce costs, and deliver enhanced customer satisfaction.
Challenge 3: Maximizing Machine Productivity
Optimizing machine productivity is crucial for meeting production targets and maximizing overall efficiency. However, manufacturers often find themselves facing a common dilemma – how to ensure greater yields from machines without sacrificing their reliability. This challenge poses significant risks and can result in losing precious production capacity and wasted time for skilled technicians.
Two common mistakes manufacturers make in addressing this challenge are worth highlighting. On one hand, some manufacturers push their machines to their limits in an attempt to extract every ounce of productivity, only to encounter frequent breakdowns during critical jobs. This approach compromises the reliability and longevity of the machines, leading to costly repairs and unplanned downtime. On the other hand, some manufacturers follow scheduled preventative teardowns of maintenance repair and overhaul (MRO) items according to manuals, only to discover that these components are still in acceptable operating condition. This results in unnecessary disruptions to production and wasted resources.
Solution: Leveraging MES for Optimal Maintenance and Reliability
Implementing a manufacturing solution with MES capabilities proves to be a more effective approach to address the challenge of maximizing machine productivity while maintaining reliability. An MES enables manufacturers to measure true output and determine the optimal maintenance schedule, resulting in prolonged equipment life and the avoidance of unnecessary production line shutdowns. By combining real-time production and process monitoring data with predictive analytics, an MES empowers manufacturers to accurately determine when maintenance, repair, and overhaul (MRO) updates are truly necessary.
By leveraging sensors and predictive analytics, an MES can detect anomalies and potential disruptions in production. For instance, variations in motor current, unusual vibrations, fluctuations in pressure, or temperature rises can indicate potential issues. By monitoring and analyzing such events in real-time, employees gain factual insights into asset “health” and can proactively manage production risks. This approach allows for establishing application-appropriate maintenance schedules based on actual equipment usage within a specific plant.
According to industry statistics, implementing predictive maintenance through an MES can result in significant benefits. A study by Deloitte reveals that predictive maintenance can reduce maintenance costs by up to 25% and decrease machine downtime by 45%. Additionally, the use of real-time analytics can lead to a 30% improvement in labor productivity. These statistics highlight the transformative impact an MES can have on optimizing machine performance, reducing unplanned downtime, and improving overall operational efficiency.
Wrapping Up
We hope this blog has shed light on the common challenges manufacturing organizations face and the potential solutions to overcome them. As you navigate the manufacturing maze, we encourage you to take proactive steps to overcome these challenges and embrace digital transformation’s benefits.
We would love to hear about your own experiences and insights regarding manufacturing challenges and solutions. Have you encountered similar issues in your organization? What strategies have you implemented to address them? Share your thoughts, success stories, and lessons learned by emailing us at contact@eworkplace.com. Your experiences can inspire and guide others on their manufacturing journey.
If you have any questions or need further assistance, our team is here to help. Feel free to ask any specific questions about the challenges discussed or seek additional guidance on implementing the Smart Factory solution in your manufacturing processes.
Ready to add Smart Factory to your portfolio and differentiate yourself from competitors? Schedule an appointment with us today to discuss how we can partner up!