How does one distinguish between scheduling and planning?
What is the purpose of production planning?
Why Is production planning essential?
How does production scheduling work?
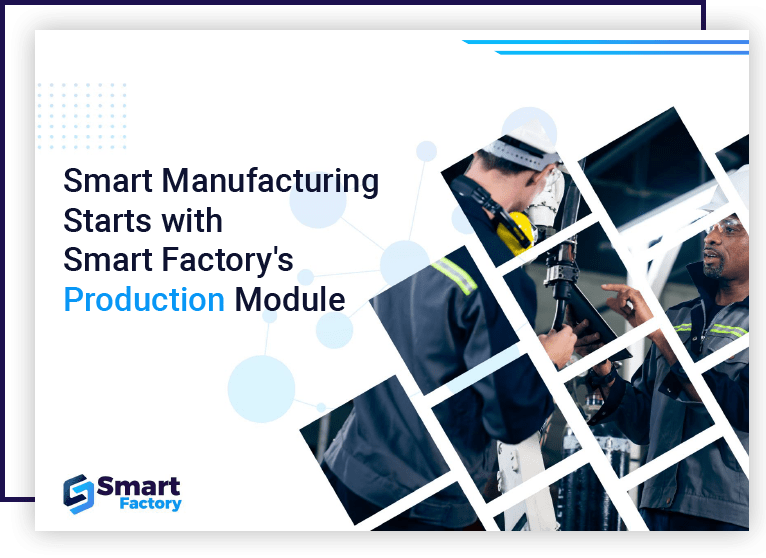
Optimize Your Production Process With Our Production Module
Production Planning Types

Work Process
The task method is frequently employed when creating a distinct production plan for a single product. Although it can also be used in more extensive manufacturing facilities, this production planning technique is typically utilized in smaller-scale processes. The work technique is particularly beneficial when a product or service requires specific customizations.

Batch Production Method
This approach involves producing items in batches rather than individually or continuously. The batch production method works well when delivering goods on a large scale.

Flow Technique
A demand-based manufacturing strategy known as the flow method shortens the lead time for production by increasing line speed. Work orders serve as the basis for the beginning of the production process, which continues without interruption until all finished goods are produced. By utilizing machinery and minimizing human intervention, wait time is reduced in what is known as continuous manufacturing.

Process Approach
The process technique is essentially an assembly line, which is what most people imagine when they think of production. When using the process technique, various types of machinery often carry out independent duties to assemble the final goods.

Mass Production Method
The primary goal of the mass production approach is to generate a steady stream of similar goods. Although done on a much larger scale, which lowers production costs, it is comparable to the flow method. When efficiency is not as crucial as uniformity, you must employ "standardized processes" to ensure that every product has the same precise appearance.
Importance of Production Planning and Scheduling and Planning
Fulfilling Clients' Needs
Best Use of Available Resources
Budgetary Management
Enhanced Productivity
Informed Decisions
Teamwork and Coordination
The Ability to Grow and Scale
Constant Enhancement
Production Schedule and Planning Stages
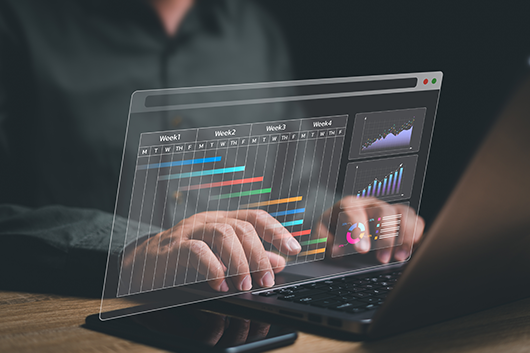
Forecasting Demand and Capacity Planning
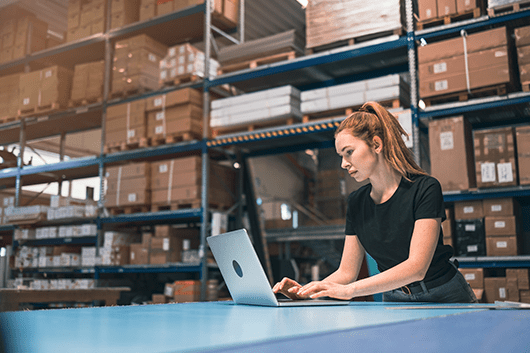
Planning and Acquiring Materials
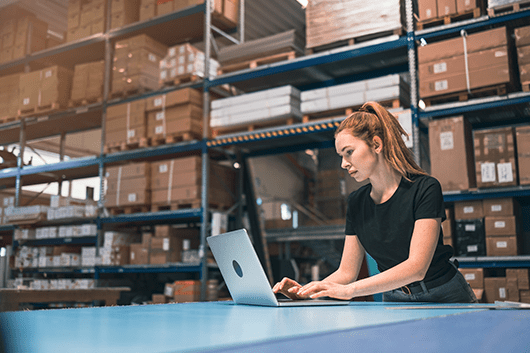
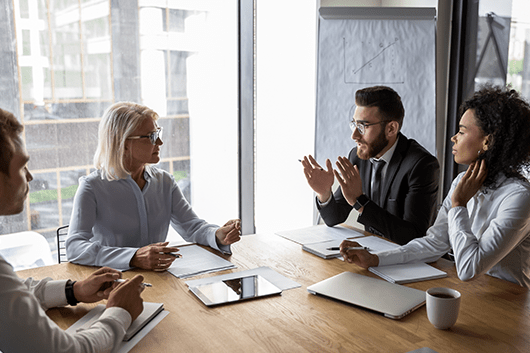
Planning and Resource Distribution
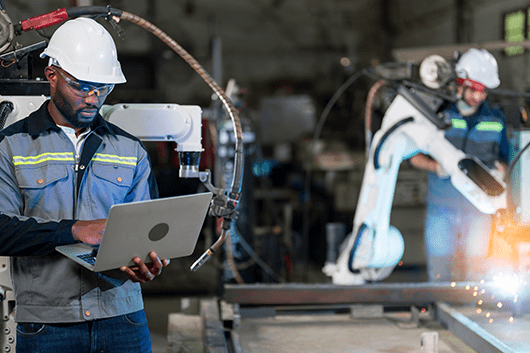
Control and Surveillance of Production
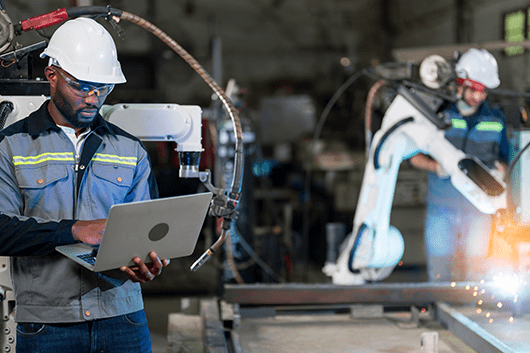
How Is a Production Plan Made?

Calculate/Project Product Demand
Understand product demand planning to choose the right method for your organization. Employ various sales forecasting strategies to gain insights into the future demand for your goods.

Optimize Inventory
Accessing inventory involves more than just taking stock. Create an inventory management plan to handle inventory efficiently, focusing on inventory control and management procedures to prevent shortages or waste.

Establish a Production Budget
Develop a production budget to determine the number of units needed to meet customer demand for a specific period. Analyze current product inventory, production capacity, sales projections, and the desired ending inventory. Apply the production budgeting formula to determine the required production level.

Planning of Resources
Understand the specifics of resource planning in the manufacturing process. Consider minimal workforce and raw material requirements, along with the machinery and systems necessary to execute your manufacturing plan.

Determine Production Costs
Estimate the cost of production based on the determined output level and required resources. Confirm that the production method will be profitable before finalizing the production plan.

Make a Timetable for Production
Create a production schedule considering production capacity, budget, and sales estimates. A production schedule is essential for ensuring the timely delivery of items and directing efforts in areas like supply chain management and logistics.

Production Management
Monitor production progress, compare it to the schedule and resource management estimates, and record findings. Continuous production control throughout the process is crucial for the success of the production plan.

Modify the Strategy to Boost Future Production Efficiency
In the final phase, use the knowledge gathered during production to devise a plan of action for improving future production plans. While production planning involves manufacturing goods or services, it should also serve as a learning tool for future, more effective production plans.
Top Companies implementing production planning/scheduling practices
Company Name | Production Planning/Scheduling Practice |
---|---|
Ford Motor Company | Implemented the Ford Production System (FPS to achieve high productivity and maintain quality standards efficiently |
Nike | Collaborates closely with suppliers and partners to optimize production processes, reduce lead times, and enhance finished product quality |
General Electric | Incorporated digital technologies into its production planning system to enhance forecasting, production scheduling, and inventory management |
Procter & Gamble | Integrated production planning with supply chain management to optimize production, reduce lead times, and improve inventory management |
Boeing | Utilized advanced production planning techniques to manage complex manufacturing to ensure quality standards and maintain delivery schedules |
Toyota | Implemented the Toyota Production System (TPS), fostering collaboration between management and employees to eliminate waste, improve efficiency, and maintain quality |
Samsung | Utilized advanced analytics and data visualization in production planning to optimize manufacturing processes and enhance product quality |
Coca Cola | Integrated production planning with supply chain management to ensure timely deliveries in the right quantities and locations |
Nestle | Applied advanced forecasting and production planning techniques to optimize production processes, reduce costs, and enhance product quality |
Amazon | Relies on advanced analytics, automation, and machine learning in its production planning, optimizing manufacturing processes and improving inventory accuracy |