Manufacturers must be able to manage their business effectively rather than just creating a product. If they can’t, they won’t be able to run a profitable business. Factory operations management is critical—it keeps the lights on.
Of course, there is more to industrial operations management. Before we get into the benefits of manufacturing operations management, let’s define the term and the areas covered.
Manufacturing Operations Management: What Is It?
Domains in Manufacturing Operations
As mentioned, the procedures and actions involved in converting raw materials into completed goods are manufacturing operations. Understanding the fundamentals of manufacturing operations is essential before one can comprehend manufacturing operations management. The manufacturing operation categories are described below.

Management of the Supply Chain
One essential component of manufacturing operations is the supply chain. Managing vendor relations, overseeing shipping, distribution, and delivery procedures, optimizing inventory, and handling other logistical activities are all included in managing physical commodities and their logistics. However, it covers much more ground, encompassing work-in-progress (WIP), inventory control, production scheduling, capacity planning, demand forecasting, and various other industrial activities.

Planning of Resources
Resources, including labor, equipment, and raw materials, are scheduled to be where they are needed when they are required, using a manufacturing system called resource planning, which is another facet of manufacturing processes. Resource planning aims to accomplish this as effectively as possible. This is made possible by having precise production schedules, which also help to reduce expenses and make the best use of the available resources.

Production Planning and Control
Production planning and control focuses on managing schedules, including labor, raw materials, work centers, machinery, and the entire production process. It determines the optimal strategy for producing goods within the lead time required. Output is tracked and performance is evaluated through various channels. This enables managers to verify that production is proceeding according to plan and, if it isn't, to reallocate resources to restart it.

Manufacturing Engineering
Manufacturing engineering is the application of industrial engineering tools and processes to ensure that the manufacturing of a product is as efficient as feasible in terms of quality, timeliness, and cost.

Quality Control
Suppose production does not achieve the required quality. In that case, it is not successful regardless if the schedule and budget was met. Quality control is used in manufacturing activities to inspect the product throughout the manufacturing process. It tends to concentrate on what's happening at the machine or assembly level to detect, record, and categorize faults, rectifying them swiftly and avoiding repetition.

Maintenance
Numerous resources, such as machinery, are used in production; this equipment must be in working order to avoid expensive delays. Upkeep constitutes a crucial component of equipment for production. Anticipating problems and being prepared to address them promptly is essential. The regular maintenance of machinery and equipment reduces risk management.

Inventory Management
Keeping an adequate supply of inventory is another essential aspect of maintaining a production line. The planning and ordering of supplies and parts required for production is known as inventory management. It also handles how those materials and components are stored, setting up a system for monitoring stock levels and placing new orders before stock runs out.

Logistics Management
The organization and management of the movement and storage of raw materials and completed goods inside the production facility form the core of manufacturing logistics. This complicated operation involves many tasks, from transferring raw materials to production lines, transporting completed goods to a warehouse, and finally shipping those goods to clients via various distribution channels.
Types of Operations Management (OM)
Operations management comes in various forms. The responsibilities of an operations manager might differ significantly depending on the industry and the size of the business. They could have a broad range of duties or focus on only one. Let’s discuss below the different tasks performed under operations management.
- Design and Development of Products: In OM, developing a new product or enhancing an existing one is known as product design and development. This encompasses idea generation, research, design, testing, and production. Lastly, it includes product management, marketing, and packaging.
Market analysis, product design, testing, prototyping, and launch are all included in this process. The process aims to design and develop a product with the needs of the customer in mind. Customers must find it affordable, but the business must also make money from it.
- Purchasing and Acquiring : It’s the procedure of acquiring products and services from vendors for use within a company. It entails market research, assessing bids, supplier selection, and contract negotiations. This process is essential to ensuring enterprises have the resources to produce goods.
- Forecasting : Forecasting is predicting demand for a good or service using past performance and current trends information. Businesses can use it to plan their operations and output to satisfy customer demand. It helps to reduce waste as well.
Organizations use forecasting to plan their inventory and staffing levels and their capital expenditures to improve productivity and earnings.
- Planning Capacity : A company must adapt to the shifting needs of its customers. It is a crucial component of operations management because it seeks to satisfy consumer demand while minimizing expenses.To prepare for future production, capacity must first be determined by analyzing present output. After that, plans for addressing added requirements are developed. Increasing capacity can be accomplished using the following methods:

Mechanization

Purchasing new equipment

Adding more employees
- Quality Assessment : Quality Assessment focuses on evaluating the quality of the goods and services a company produces. It entails determining the client’s needs and creating plans to put quality assurance procedures into practice to meet those needs.
- Procedure Administration : Procedure Administration involves creating and overseeing the procedures that result in products. It determines client demand and identifies the most economical ways to satisfy that demand.
- Inventory Management : Inventory management includes supplies, finished goods, and raw materials. It entails inventory level planning, monitoring, and control.
- Project Management : Project management includes planning, scheduling, and task execution of the project. This category involves deciding on project objectives, creating project plans, and keeping track of the project’s advancement.
- Supply Chain Management : This kind of operations management begins with the procurement of raw materials and ends with the delivery of completed goods.
- Lean Manufacturing : Lean manufacturing is the systematic elimination of waste from production. Lean manufacturing aims to eliminate as many needless resource expenditures as possible.
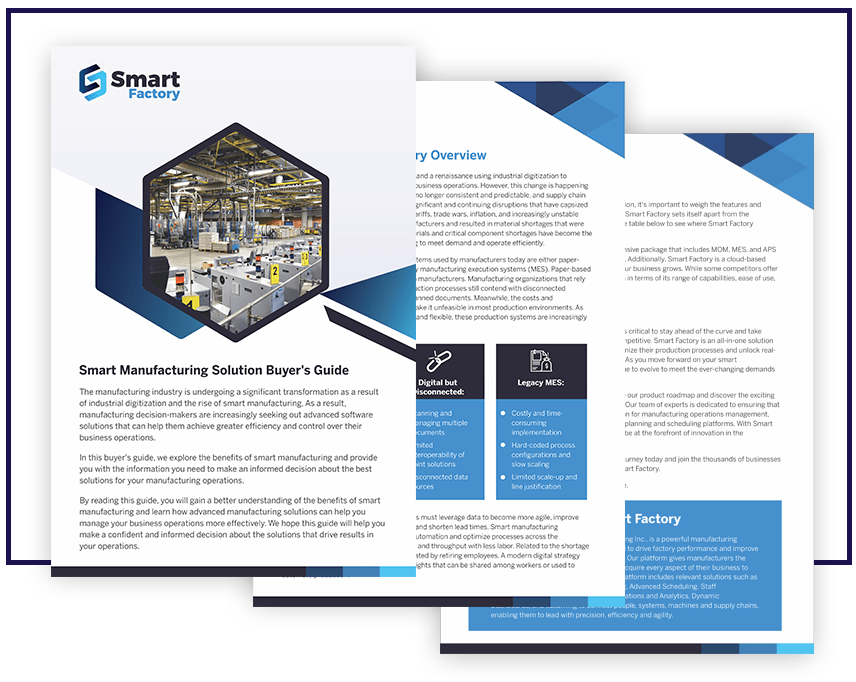
We help you to select the best option
Advantages of Operations Management in Manufacturing
Manufacturing operations management needs to monitor and manage all of these above-mentioned processes to function as a whole, deliver goods to clients on schedule, and provide profit margins for manufacturers. This allows them to continue operating and growing. Of course, there are other advantages as well, as mentioned below.
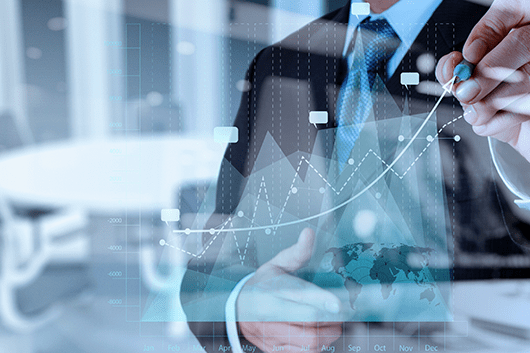
Competitive Edge
Every kind of asset’s data, regardless of its location or source, is included in a centralized perspective of the operational process. With just one blueprint, asset performance can be logically tracked, maintenance and inspection schedules can be made, and productivity disruptions can be kept to a minimum.
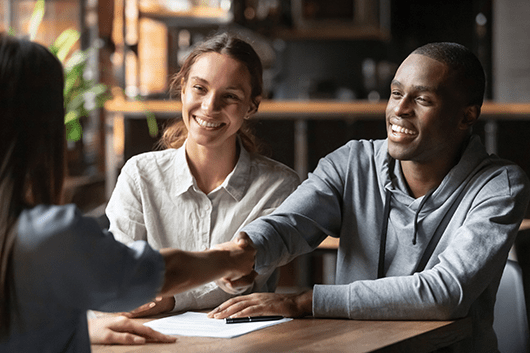
A Rise in Profitability
Manufacturing operations management is beneficial since it allows a company to focus more time and resources on generating new ideas that will boost sales or result in creating new products by ensuring that production and operations management run smoothly. You can’t concentrate on other areas that can increase your sales and market share if you’re constantly putting out fires and running your business behind schedule.
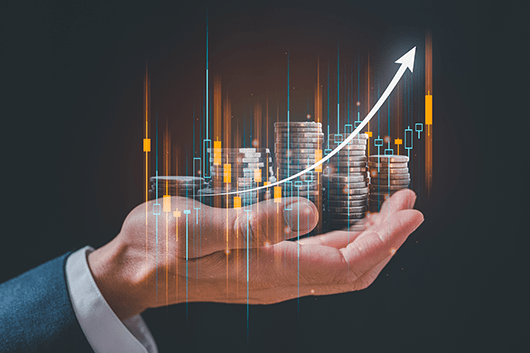
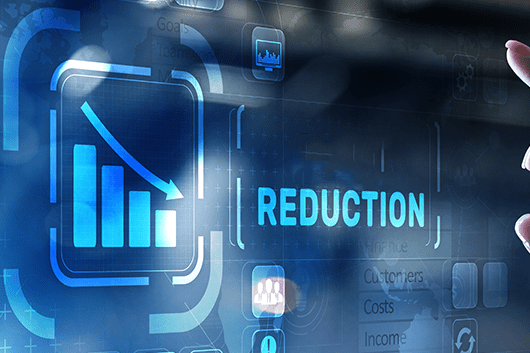
Waste Reduction
Cutting down on industrial waste has many advantages. Manufacturing activities, for instance, can aid in inventory control, enabling a business to keep the supplies it needs on hand to meet rising client demand. By increasing inventory accuracy, it can also aid in lowering the amount of storage space required. As a result, expenses are reduced and process efficiency is increased.
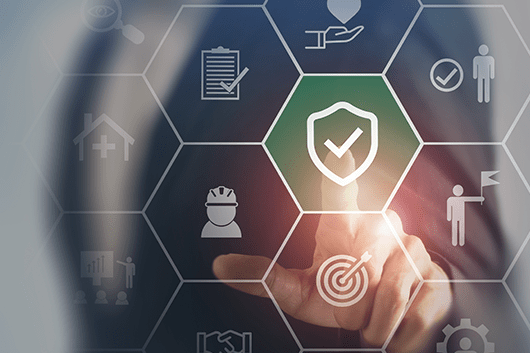
A Higher Caliber Product
By effectively managing your manufacturing activities, including material storage, you can maximize production efficiency while reducing errors in the final product. High quality products results in increased customer satisfaction. Additionally, you’ll have more time to research and create upgrades to satisfy clients’ needs.
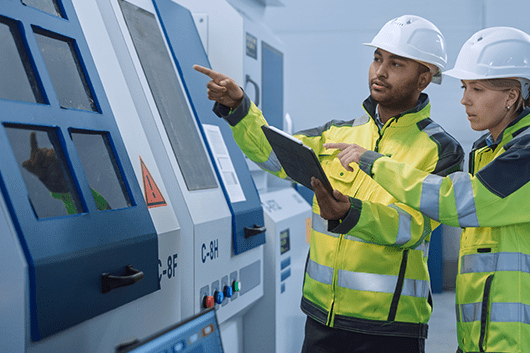
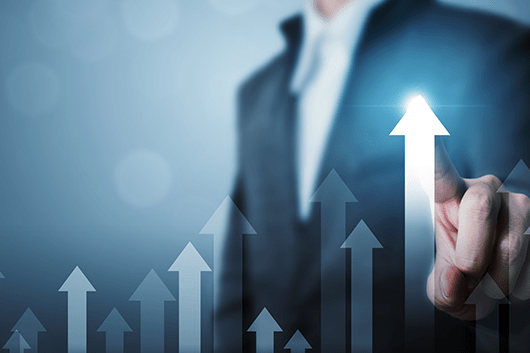
Increased Adherence
Adherence to state and federal rules is frequently necessary while manufacturing commodities, particularly in the case of food, beverage, and pharmaceutical production. Manufacturers who use manufacturing operations management assign department heads to ensure their work is done legally. In addition to making businesses compliant, this shields them from future legal action and fines, which may be expensive and damage your company’s reputation.
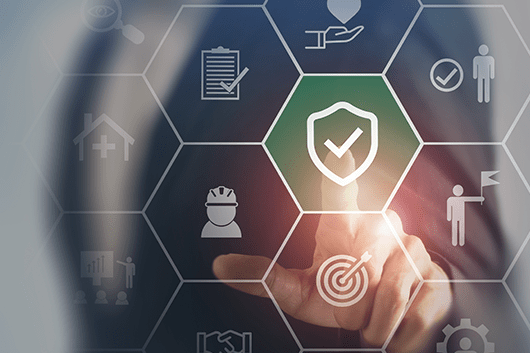
Communication Improvements
When factory operations management is involved, even teams exhibit improvements. The system’s design fosters collaboration among departments, allowing them to work more effectively. Again, all of these advantages feed into one another to create a continual cycle of progress, with each benefit building on the previous one.

How Is the Customer Experience Affected by Operations Management?
Operations management greatly influences the customer experience, encompassing the control, direction, and planning of the production process and related activities.

Boost Customer Satisfaction
A company's operations can be managed to ensure client satisfaction, by addressing things like safety and product quality. Operations management enables businesses to understand the requirements and expectations of their customers, contributing to enhanced satisfaction.

On-Time Deliveries
Improving the customer experience involves developing processes for on-time product delivery. Businesses utilizing operations management can provide prompt product delivery by keeping production smooth for fewer client complaints.

Boost Client Loyalty
Efficient procedures, increased quality, and timely deliveries developed through operations management enable businesses to increase client loyalty. Consumers will be more satisfied with the products and will come back to purchase again.

Facilities
Utilities have a combination of fixed and linear assets, so they have to make sure that workers and equipment are protected while providing services to their communities. Facilities include power plants, plants, and isolated, inhospitable outdoor areas where assets are dispersed. By offering continuous data management and documentation, benchmarking capabilities, and cooperation on planned and operational asset performance, EAM supports the industry's reliability-centered maintenance paradigm.
Wrapping up
Operations management is an essential component of any organization, ensuring the smooth and effective operation of the business. It is crucial to have the appropriate individuals managing operations and implementing the proper procedures and structures.
Efficient operations management can boost an organization’s productivity, minimize expenses, and increase customer satisfaction. With a thorough grasp of the business’s activities, necessary adjustments and enhancements can be made to ensure the best possible results.