Trends in Smart Manufacturing by 2024
Smart Factories Transforming Shop Floors and Operations
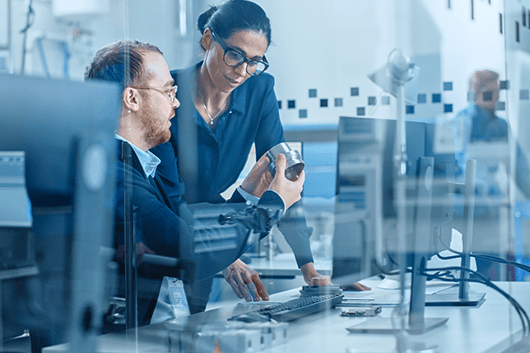
Higher Caliber of Product
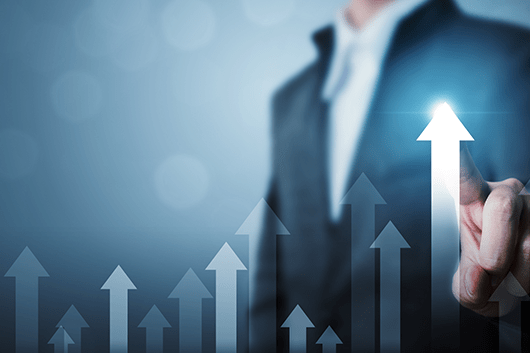
Better Efficiency
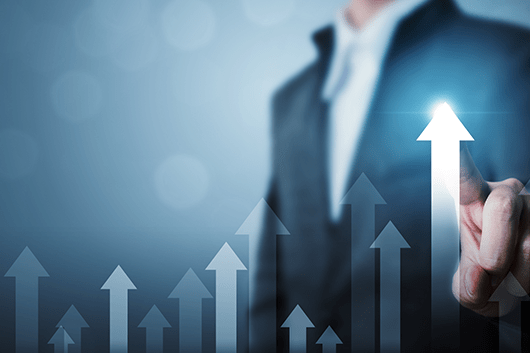
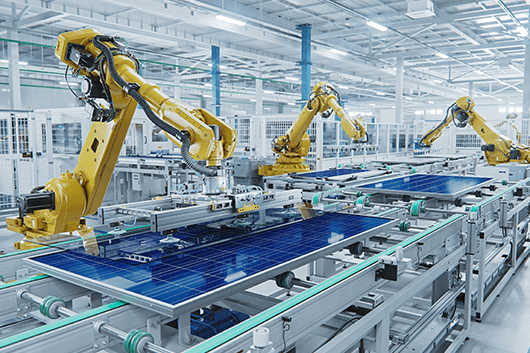
Long-Term Sustainability
Better Decision-Making Enabled by Digital Twin Technology and Predictive Maintenance
Reshoring Gains Momentum Amid Supply Chain Issues

Decreased Transport Expenses
Production taking place domestically results in a significant reduction in the expenses and duration of international product transportation. Reshoring benefits automakers like Tesla, allowing them to manufacture vehicles closer to their primary market, thereby lowering logistics costs and time.

Control of Quality
Reshoring allows greater control over production procedures and closer oversight, ensuring a consistently high-quality final product. For instance, Apple has returned part of its manufacturing to the United States to strictly oversee the quality of its products.

Time to Market
Domestic manufacturing can significantly shorten the lead time from production to market, enabling quicker responses to market developments. The adaptability of restored manufacturing was evident when many US corporations pivoted to locally produce ventilators during the COVID-19 outbreak in response to unexpected demand.

Local Employment Generation
Reshoring contributes to regional economies by generating jobs. For example, General Electric moved some of its appliance manufacturing operations back to Kentucky, positively impacting its economy and creating several hundred new jobs.
Addressing Labor Shortages: Manufacturers Reskill Employees and Raise Wages
- Raising Income: Manufacturers are considering increasing compensation to attract and retain qualified workers as the talent shortage becomes more apparent. According to a poll conducted by The National Association of Manufacturers, approximately 75% of manufacturers planned to increase pay by 3% in 2022.
- Upskilling and Reskilling: The workforce must possess strong technical and digital skills due to the growing use of digital technology in manufacturing. According to workers under 25, career opportunities (65%) and training and development (69%) are the main reasons people continue with their current workplace.
Industry Push for Carbon Neutrality from Manufacturing Companies

Enhanced Brand Worth and Reputation
A manufacturer's brand value and consumer loyalty grow when they commit to becoming carbon neutral, showcasing their dedication to environmental responsibility. Patagonia is a well-known outdoor apparel brand with a solid reputation for environmental stewardship, offsetting its carbon emissions and supporting sustainable practices.

Operational Efficiency and Cost Savings
The transition to carbon neutrality often involves adopting energy-efficient technology and streamlining procedures, reducing energy usage and cost savings. Interface, a multinational maker of modular flooring, provides an example of this by implementing energy-efficient measures, resulting in a 96% reduction in carbon emissions and significant cost savings.

Gaining Entry into Novel Markets and Clientele
Achieving carbon neutrality enables producers to connect with consumers who prioritize sustainability and enter emerging markets. The global consumer goods giant Unilever experienced increased market share and achieved carbon neutrality throughout its operations by meeting consumer demand for sustainable products.

Operational Efficiency and Cost Savings
The transition to carbon neutrality often involves adopting energy-efficient technology and streamlining procedures, reducing energy usage and cost savings. Interface, a multinational maker of modular flooring, provides an example of this by implementing energy-efficient measures, resulting in a 96% reduction in carbon emissions and significant cost savings.
Successful Strategies Adopted by Specific Manufacturers in Making Changes
- Working Together to Reduce Carbon Emissions: Several manufacturers are forming joint ventures and external collaborations to meet strict emissions regulations for their products. They make notable progress in product decarbonization by identifying critical needs and seeking outside partners with the expertise to address them. For example, a well-known provider of industrial automation has partnered with a clean energy solutions provider to electrify mine haulage vehicles with energy storage devices, showcasing the value of strategic cooperation in promoting sustainability.
- Backing Net-Zero Emissions: Some producers are investing in electrification and other low-carbon or renewable fuel technologies for their products to achieve net-zero emissions. A major engine manufacturer, for instance, is investing over $1 billion in US dollars at its US facilities to support engines running on low-carbon fuels like hydrogen, aligning with its broader objectives for clean energy.
- Constructing a Niche Vertical: Manufacturers are electrifying their product lines, and some are establishing specialized divisions for this purpose. One of the world’s top producers of mining and construction equipment, for example, has created a dedicated vertical to develop zero-emission technologies and products, such as electrified drivetrain product lines and modular, scalable advanced power sources, to assist clients in meeting their climate-related objectives.
- Entering Adjacent Markets with Purposeful Expansion: To keep up with electrification trends, several manufacturers are focusing on nearby markets. Making strategic investments in these areas can facilitate growth and prepare for new opportunities. For instance, a leading US fabrication company prioritizes capital investment in lightweight materials to support client expansion in EVs, energy infrastructure, and renewables.